Index
Intro
S.O.E.
Mk.I .32ACP
Mk.II&IIA .32ACP
The Suppressor
Mk.I 9mm Para
Production
Distribution
The U.S. Welrod
The Sleeve Gun
Misinformation
|
THE SUPPRESSOR
At an earlier stage, SOE had already experimented with reducing the blast from an ordinary pistol but even when successful in reducing the muzzle blast, the significant noise of the weapons working parts remained. In addition, a conventional weapon fitted with a suppressor became disproportionately big and consequently difficult to conceal on ones person. The decision was therefore made to develop an uncomplicated single-shot pistol based on a rotating breech to be worked manually.
The Welrod differentiates from others in that it is constructed around an integrated suppressor. The entire mechanism is built into an 11.8 in. metal tube with a diameter of 1.26 in. The roughly 3.74 in. barrel ends in a bearing approximately halfway down the tube. Along the five-tracked rifling, 20 holes has been drilled with a .063 in. diameter, permitting the gases to escape into the containing cylinder housing functioning as an expansion chamber. The bearing, best described as a sort of baffle, is provided with 12 holes equally .063 in. in diameter, enabling the gases to further circulate from the expansion chamber and into the deflector system consisting of a series of baffles and washers.
Here a sectioned Mk.IIA, the holes perforating the barrel along the rifling can be clearly seen. Also notice the linen/leather washers are almost worn out.
The primary purpose of ventilating the barrel is usually to prevent the projectile from attaining supersonic speed thus breaking the sound barrier, and furthermore to take the edge off the vehemently expanding gases by detouring them into the deflector system where they are being cooled and slowed down before escaping through the muzzle. Calibre .32 ACP is factory born subsonic, why the ventilation of the barrel in this case merely serves to slow down the speed of the expanding gases.
Here the receiver and barrel completely stripped and with the suppressor tube removed, the holes perforating the barrel along the rifling can be clearly seen. Also note the holes in the bearing fitted onto the muzzle.
When fired, the projectile passes through 18 metal discs (baffles, see cross section and diagram below) separated by 12, 0.2 inch wide spacers and three rubber washers. The baffles are of course provided with a hole to allow the projectile to pass unobstructed, but it must be noted that three of the discs has a hole-diameter of 0.5 inch while the other 14 are but 0.37 inch across. It is extremely important when replacing the baffles that the three baffles with the wider diameter holes are placed on the outside of the washers in order to allow the washer material to expand as they are penetrated by the projectile.
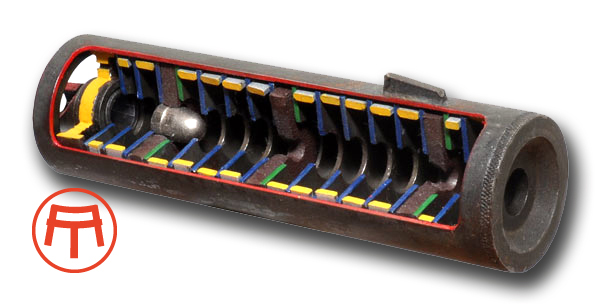 Notice that the three (green) baffles with the wider diameter holes are placed on the outside of the washers in order to allow the washer material to expand as they are penetrated by the projectile.
The three washers have no holes until penetrated by the very first shot. The purpose of these washers are to reseal them selves, if not entirely then as much as possible after the exit of the projectile, thus restraining the gases and forcing them into the deflector system. The washers are however quickly worn resulting in a significant decrease in noise reduction. This has no greater tactical influence though as the Welrod was solely meant as a liquidation weapon and new washers could be reinserted after the mission was completed.
It was however rather difficult and laborious to reassemble all the baffles, spacers and washers in the correct succession, not just because of the importance of maintaining maximum sound reduction, but also because damage to the internal parts and great bodily harm to the operator easily could occur if the baffles were stacked in reverse order. Due to lack of free space for the washer to expand, this could result in the projectile exiting through the side of the silencer tube, or it could simply get plugged up in the damaged internal parts.
Whether this was the reason for the next development I cannot say, but it is a fact that a disposable silencer unit ready to insert if needed was developed. It consists of an enclosed brass tube 1.151" in diameter and 3.536" in length. It contains all the baffles, spacers and washers, the only difference being that the discs are made from brass and the washers from solid rubber.
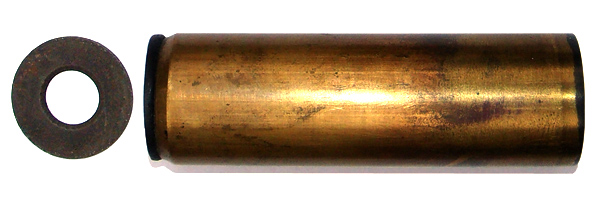
The silencer unit shown protruding from the silencer tube.The silencer units shown compared to the standard baffle and spacer stack. Notice the rubber washer has been encapsulated with a roll crimp and is protruding from the brass tube. The reason for this is to make sure that the unit will fit tight in the tube and not rattle back and forth.
With this unit in hand, all the operator has to do is to unscrew the silencer tube end-cap, extract the used unit and drop in the new one, top off with a steel disk from the old system, and then screw the end-cap back on. It’s now ready for a new mission and many more suppressed shots.
An identical disposable silencer unit measuring 1.151" in diameter but only 2.476" in length was developed for the Sleeve gun.
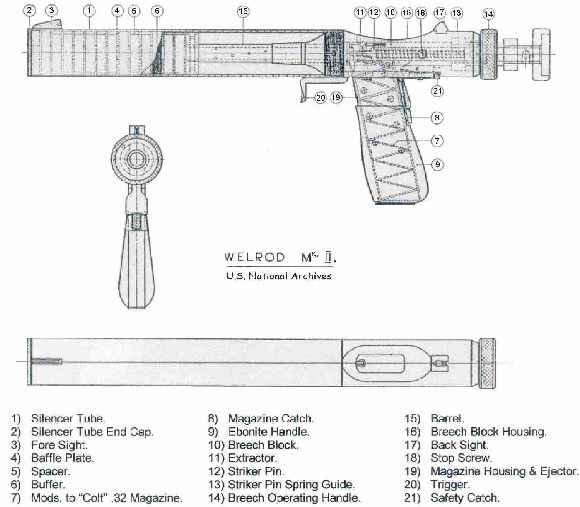
The speed of sound at a temperature of 15 centigrade travels 1.115 fps. or 340 m/s if you like. For every single centigrade rise in temperature, the speed of sound increase accordingly by 1.6 fps. (0.5 m/s.) It is therefore important to maintain a certain tolerance between the muzzle speed and the speed of sound if the optimal sound reduction is to be obtained. According to the manual, the Welrod delivers a 72 Grain Kynoch projectile at a muzzle speed of 920 fps.
DECIBEL
Reportedly the suppressor functions optimally within the first 10 – 15 rounds fired. For those who prefer dry numbers I can inform that the American OSS (Office of Strategic Service), according to a document dated February 12, 1945, performed a measurement on noise from suppressed weapons to help evaluate their own just finished prototype, Hi-Standard Automatic Pistol calibre .380 ACP. All measurements are performed at a perpendicular angle 10 ft. from the muzzle.
From the document it can be seen that the average noise level of the Welrod pistol was at 73 dB, Hi Standard .380 ACP at 81 dB and Hi-Standard .22LR at 71 dB. In comparison, a non-suppressed calibre .32 ACP pistol, has a noise level of 105 dB. This equals, in the case of the Welrod, a noise reduction of approximately 32 dB. You need to keep in mind that the decibel-scale is logarithmic as opposed to linear. From 1 dB to 3 dB you double the value, 6 dB you quadruple, 10 dB is tenfold the value and 20 dB a hundredfold. I am personally of the opinion that the decibel factor is too intangible a notion to deal with, why I much prefer an audio/visual explanation and comparison. Hence the sound of a suppressed shot is best described as the sound of a .22LR percussion cap followed by the sound of a match being struck, the match-sound being the gases slowly seeping from the suppressor. Should the operator choose to reload the weapon immediately upon discharge, the hissing sound of the gases will then be replaced by a dull “plop” as the gases are now released at once under pressure through the chamber.
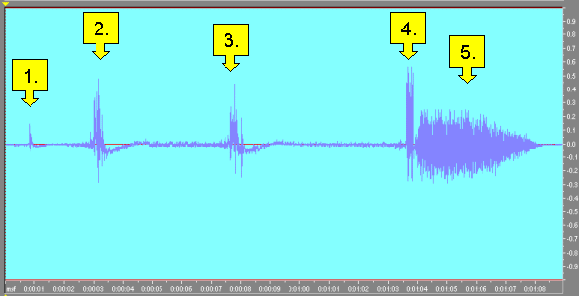
Above is a visualised picture of the sound profile generated during the loading procedure and the firing of the Welrod Mk IIA. The first short peak (1.) is the breech being twisted into the open position. The second (2.) is the withdrawal of the breech. (3.) is the breech being slid forward and twisted back into the locked position. (4.) Is the shot and (5.) is the sound of the gases slowly and under pressure seeping from the suppressor. Observe that the shot itself hardly is louder than the loading procedure.
Judge for yourself the sound of the Welrod Mk IIA: 
After firing 15 rounds or so, the efficiency of the suppressor is considerably reduced as the holes in the washers are being worn to the size of the calibre itself. In many cases, an extraction tool together with a small canvas bag containing 3 spare washers, was issued permitting the operator to change these as the need arose.
The extraction tool was a cylindrical metal rod approximately .16 in. across and 5,5 in. long. One end formed the shape of a an “L” and the other was bend in a loop. Having removed the muzzle end-cap, the L-shaped end was inserted through the washers and baffles and these could then be removed by extracting the tool with a finger through the loop. The washers came in different variants such as a .03 in. linen patch glued onto a .23 in. rubber patch. I have also come across other combinations.
|